Biodegradable stretch film increases sustainability of logistics
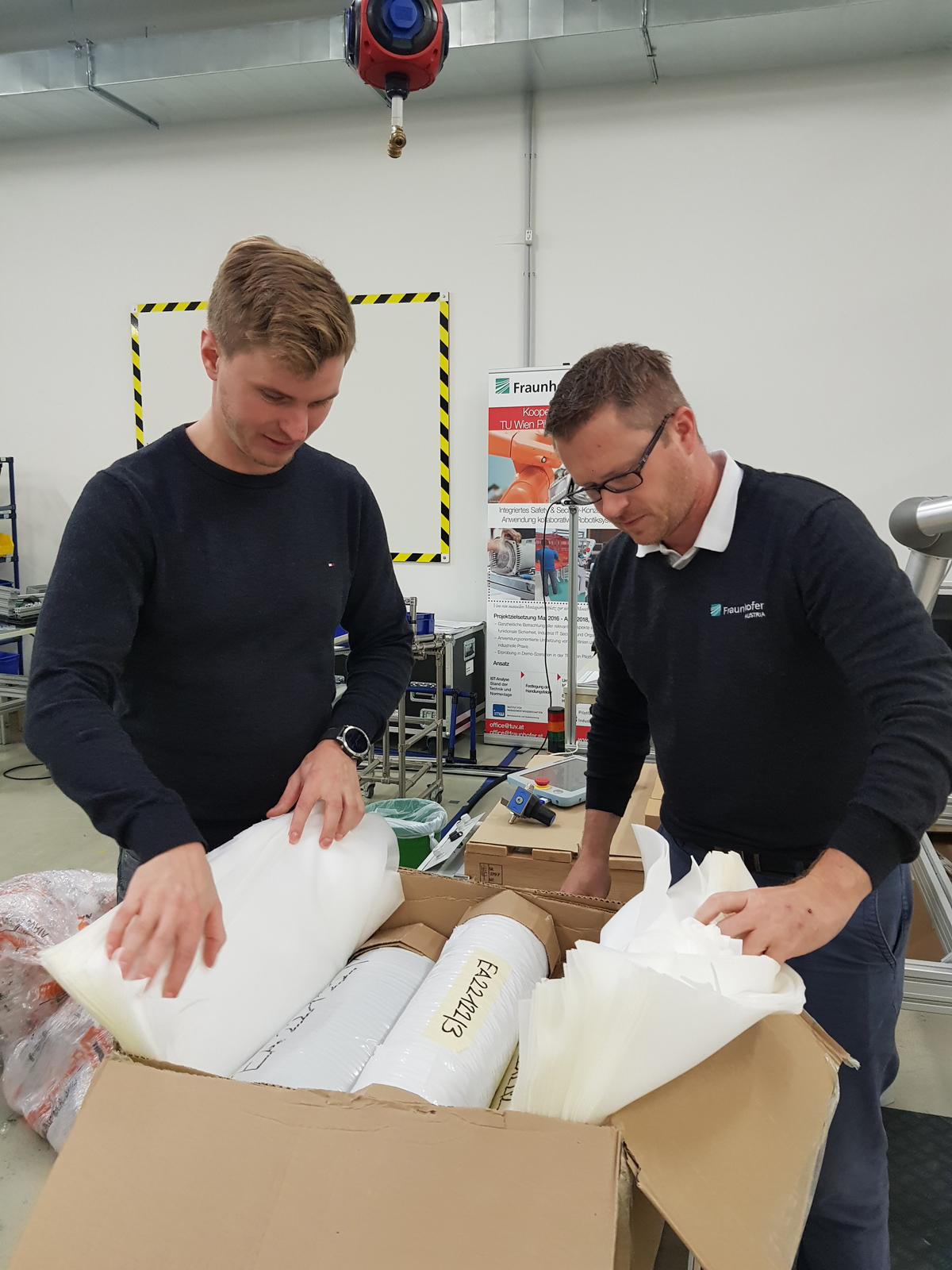
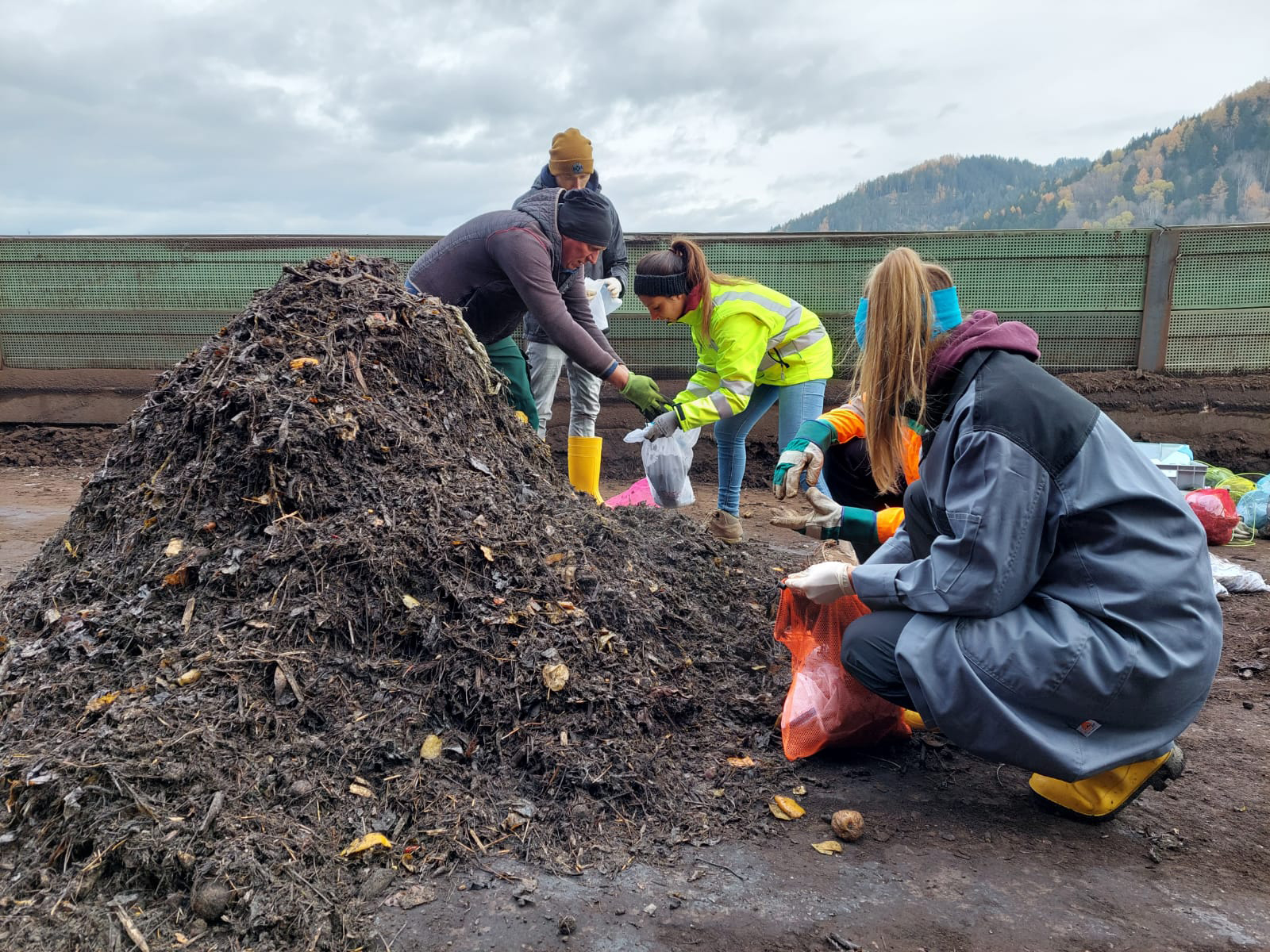
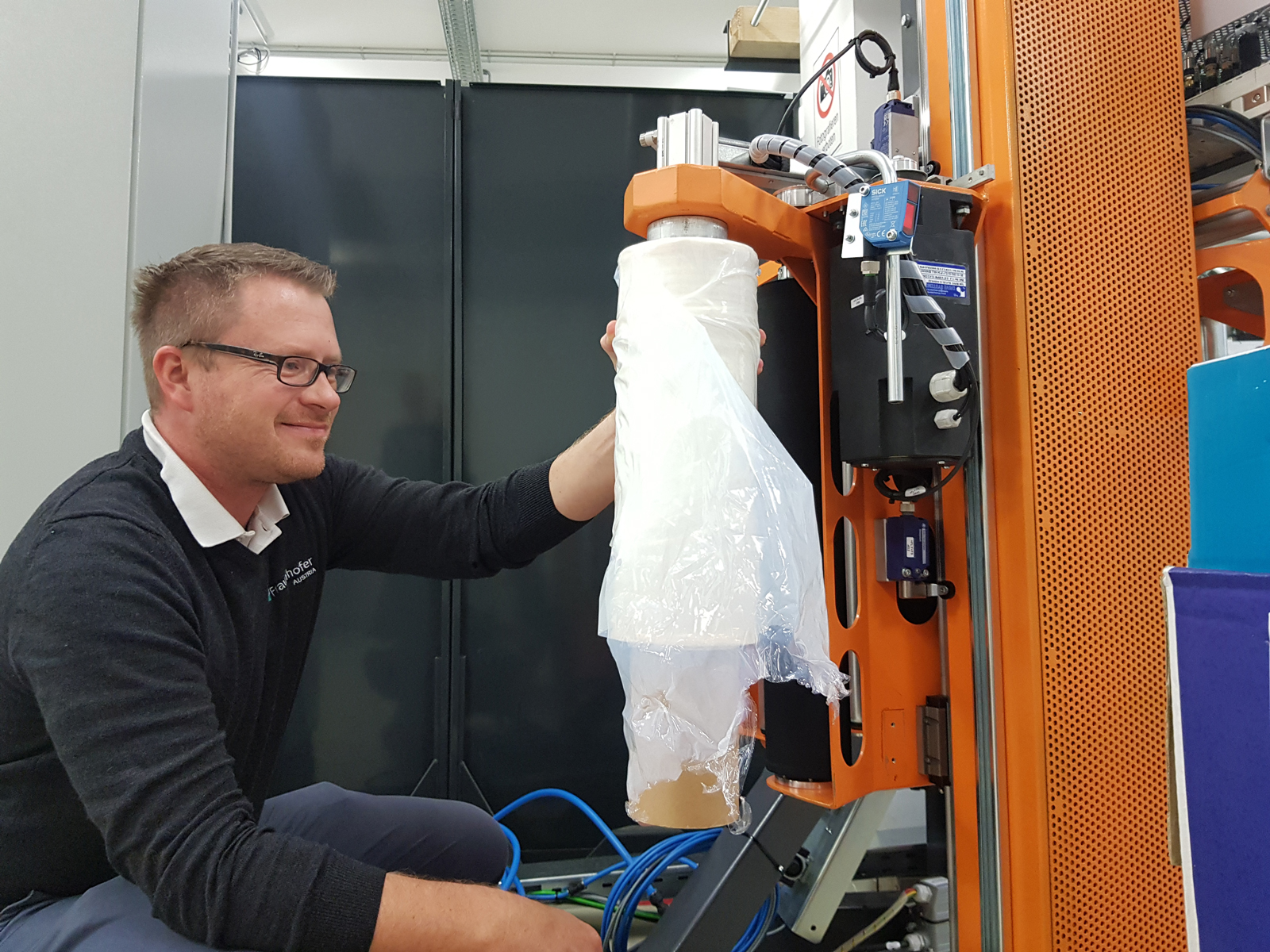
A research consortium led by Fraunhofer Austria has developed a bio-based plastic that can be composted without leaving any residue behind
Wherever goods are transported, secure packaging is a must. For pallets, stretch film made from petroleum-based plastics has become the most common choice. Used as disposable packaging, it prevents goods from slipping when the truck brakes. In the environment, the films take up to 400 years to decompose, and microplastics are often created in the process. A switch to bio-based, biodegradable films therefore offers an opportunity to significantly improve sustainability in logistics. A research consortium has now succeeded in developing such a film as part of the "EFFIE" research project funded by the Austrian Research Promotion Agency FFG. The project partners were Pamminger Verpackungstechnik, Montanuniversität Leoben, Vienna University of Technology as well as Lenzing Plastics, with Fraunhofer Austria in charge of the project.
Packaging, including pallet packaging, accounts for around 59 percent of the 25.8 million tons of plastic waste produced in Europe each year. Bio-based plastics are currently hardly used at all, or only for niche products; moreover, they are not automatically biodegradable. "Bio-based and biodegradable are two different pairs of shoes. If a plastic is called a bio-plastic, this often only means that at least one of its components consists of a renewable raw material. However, this does not mean that this plastic is biodegradable, as the definition states that a bio-plastic must either be biobased or biodegradable or have both properties. So in many cases, degradation leaves residues and can create dangerous microplastics. Our goal was to develop a plastic that is biodegradable and yet meets all the requirements for use in logistics," explains project coordinator Paul Schindler.
The project was crowned with success. The films now presented by the research consortium are biobased, fully degradable and decompose without residue within a few weeks when composted. The consortium ensured from the outset that the films would be able to meet the requirements for pallet transport. The first step at the start of the project was to draw up a carefully documented catalog of requirements for stretch films in the packaging process. More than 40 different biobased materials were then researched and reduced to the most suitable ones. From the seven favored biodegradable granulates films were produced and subjected to rigorous testing. Not only did the biobased plastics pass the practical biodegradability tests, they also showed better mechanical properties, such as higher elongation at break, than the established polyethylene. A team from the Vienna University of Technology also tested whether biomimetic structures could improve the properties and subsequently reduce the amount of material required. However, the unstructured film proved to be the better option.
PBAT polybutyrate dipate terephthalate was identified as a suitable biodegradable petroleum-based plastic. Ultimately, however, the consortium was able to develop a polylactide plastic that is both biobased and biodegradable.
The film was prototypically produced on a laboratory scale as part of the research project. Now the researchers hope that manufacturers will succeed in mass producing it for industrial application.
Economical use
Another goal of the researchers was to use less film overall during transport. Until now, pallets have in most cases always been wrapped with the same number of layers, regardless of what is stored on them. "It makes no sense at all to always wrap pallets the same way, regardless of whether they are loaded with heavy food cans or lightweight goods such toilet paper. Rather, you should be able to specify what the characteristics of the pallet are, and ideally the machine will then use only as much film as necessary and place it in the way that makes the most sense," explains Paul Schindler. This can mean wrapping a pallet more often in the lower area where heavy goods are stacked, than in the upper area, where lighter goods are located. "To put the concept into practice, we would have to work out the ideal machine parameters together with an interested party," explains Paul Schindler. Project partner Pamminger Verpackungstechnik has developed a machine for this purpose, which is able to adapt to the pallet load by means of control technology. The wrapping tension on the pallet is tension-controlled by this new development, thus avoiding tension peaks at the corners. Compression-sensitive products can be packaged safely, and film tension fluctuations are not an issue any more. Adaptation to the respective characteristics of the biodegradable films is optimally possible.
Samples of the films as well as the patented machine can be inspected by guests at the closing event of the EFFIE project on September 12, 2023 at the TU Vienna pilot plant. Registration is required via email to paul.schindler@fraunhofer.at